Der neue FMEA-Standard – Fragen von Unternehmen22 | 04 | 20
Die Fehlermöglichkeits- und -einflussanalyse (kurz FMEA) ist ein methodisches Vorgehen, um entwicklungsbegleitend potenzielle Risiken in Systemen, Produkten und Prozessen zu finden. Damit ist die FMEA aus der Qualitätssicherung nicht mehr wegzudenken. Sie wird insbesondere in der Design- bzw. Entwicklungsphase neuer Produkte oder Prozesse angewandt. Von Lieferanten von Serienteilen für die Automobilbranche sowie anderen Industrien wird sie mittlerweile sogar explizit gefordert.
Das gemeinsam von AIAG und VDA erarbeitete FMEA-Handbuch zur Harmonisierung ihrer bisherigen Vorgehensweisen ist seit fast einem Jahr veröffentlicht. In Trainings und im Kundenkreis begegnen mir seitdem stets typische Fragen wie:
- „Was bedeutet der neue Standard für unser Unternehmen?“
- „Was bringt uns der neue Standard konkret?“
und vor allem:
- „Müssen wir alle bestehenden FMEAs überarbeiten und wenn ja, bis wann?
Was bedeutet der neue FMEA-Standard für unser Unternehmen?
Bisher mussten vor allem international agierende Unternehmen mehreren Standards gerecht werden. Durch das Bilden einer weltweit einheitlichen Vorgehensweise wird die Komplexität im Qualitätsmanagement deutlich reduziert – das ist ein nicht zu unterschätzender Vorteil. Diese Vereinheitlichung erleichtert Teams die internationale Zusammenarbeit, sowohl unternehmensintern, als auch mit Kunden und Lieferanten. Die Durchgängigkeit der Methode gibt dem Team in Entwicklungsprojekten zudem mehr Sicherheit in ihrer Anwendung sowie in der Bewertung von Risiken.
Was bringt der neue Standard konkret?
Hier sind zwei Aspekte hervorzuheben. Einer ist die Rolle des Managements.
Das Management wird im neuen FMEA-Prozess deutlich stärker involviert als dies bisher der Fall war. Dies ist ein wichtiger Impuls und wesentlicher Vorteil für die ausführenden Teams, denn für die Anwendung der Methode trägt das Management die Verantwortung. Ihr Engagement ist entscheidend für den erfolgreichen Einsatz der FMEA. Dazu gehören neben der Bereitstellung ausreichender Ressourcen auch die aktive Beteiligung der Produkt- und Prozessverantwortlichen. Außerdem ist insbesondere die Akzeptanz der identifizierten Risiken und die Umsetzung der Maßnahmen durch das Management maßgebend. Im Handbuch wird zudem empfohlen, dass bei entsprechenden Bewertungsresultaten das Management aktiv einbezogen wird. Dies beginnt bei der Begutachtung und geht hin bis zur Empfehlung von Maßnahmen.
Der zweite Aspekt sind die wesentlichen Neuerungen zur Priorisierung in der Risikoanalyse.
Mit der bisherigen Vorgehensweise zur Berechnung und Bewertung der Risikoprioritätszahl (RPZ) waren viele meiner Kunden unzufrieden. Sie nannten beispielsweise Schwierigkeiten bei der Anwendung der RPZ, weil die Gleichgewichtung der Bewertungskriterien zu Fehlinterpretationen führen konnte. Zur Beurteilung eines Risikos war die RPZ nicht ausreichend. Daraus resultierte häufig die Unsicherheit, ob die vorgenommenen Bewertungen und deren Interpretationen richtig waren. Zudem bemängelten meine Kunden wiederholt, dass Möglichkeiten zur Bewertungsanpassung geboten (und genutzt) wurden, um die Brisanz eines Themas ggf. abzuschwächen. Mit womöglich fatalen Folgen!
Was wurde geändert? Auch im neuen Standard werden die Bedeutung, das Auftreten und das Entdecken eines Fehlers mit einer Skala von 1 bis 10 bewertet. Die dahinterliegenden Kriterien zur Bewertung wurden harmonisiert. Dies hat bereits eine größere Sicherheit in der Anwendung und in der Vergleichbarkeit von Bewertungen zur Folge. Eine weitere wesentliche Verbesserung liegt in der nachfolgenden Priorisierung. Wurden bisher durch die RPZ die Risiken priorisiert, erfolgt nun die Priorisierung der Maßnahmen zur Risikoreduzierung. Anhand einer vorgegebenen Matrix werden Aufgabenprioritäten (AP) in „hoch – mittel – niedrig“ eingeordnet, wobei alle Kombinationsmöglichkeiten der Bewertungen von Bedeutung, Auftreten und Entdecken berücksichtigt werden. Der Bedeutung der Fehlerfolge wird das größte Gewicht gegeben, dann dem Auftreten der Fehlerursache und danach der Entdeckung der aufgetretenen Fehlerursache und/oder der Fehlerart. Mit dieser Logik wird der Fokus besonders auf die Fehlervermeidung gelegt. Die Nachteile einer Gleichgewichtung sind ausgeräumt.
Müssen alle bestehenden FMEAs überarbeitet werden – und bis wann?
Ein klares NEIN. Ausgenommen hiervon sind unternehmensinterne Festlegungen oder entsprechende Vereinbarungen mit den Kunden. Im Handbuch wurden hinsichtlich der Überarbeitung vorhandener FMEAs und der Anwendung der neuen FMEA-Methode Übergangsregelungen formuliert:
- Vorhandene FMEAs können bei Aktualisierung in ihrer ursprünglichen Form belassen werden.
- Werden vorhandene FMEAs als Grundlage für neue Projekte verwendet, sollte das Format angepasst werden.
- Neue Projekte sollten die neue Methodik anwenden, sofern keine andere unternehmensinterne Vorgehensweise bestimmt wurde.
Mein Fazit
Aus Praxissicht lässt das gemeinsam von AIAG und VDA erarbeitete FMEA-Handbuch eine deutlich effektivere und auch effizientere Methodenanwendung zu. Dadurch kann eine höhere Akzeptanz der FMEA-Methodik erreicht werden. Konsequent vom Management unterstützt und für neue Produkte und Prozesse eingesetzt, kann der Nutzen für Produktivität und Produktqualität deutlich gesteigert werden.
Über den Autor: Ulrike Nöcker
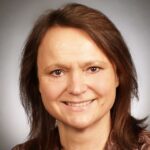