Zwischen Kundenzufriedenheit und Haftungsfall – Funktionen und Regelungen zu Reklamation und zum Umgang mit Fehlern in der Automobilindustrie22 | 11 | 22
Im Ernstfall muss es schnell gehen: Wenn die Reklamation eines Kunden eintrifft, bleiben oft nur wenige Tage Zeit, um Analysedaten zu erstellen, Maßnahmen zu treffen und zu dokumentieren sowie den Ursprung und die Ursache eines Fehlers zu ermitteln. Wenn zudem auch noch ein Produktsicherheitsrisiko besteht, wird das Ganze noch brisanter. Dann sind auch Behörden mit im Spiel und die Einhaltung von Gesetzen wird geprüft. In jedem Fall kann eine begründete Reklamation kostspielig werden.
Es lohnt sich daher, vorbeugend bereits in der Phase von Planung und Entwicklung Fehlerrisiken zu betrachten und zu minimieren. Verfahren wie APQP, Reifegradabsicherung und Methoden wie FMEA stellen wichtige und wirksame Hilfestellungen dar, um potenzielle Probleme so früh wie möglich zu erkennen und abzustellen. Die Freigabeverfahren PPAP und PPF sind ebenfalls zu erwähnen. Sie leiten dazu an, ein Projekt vom Ende her zu denken – wobei mit „Ende“ hier der SOP (Start of Production) gemeint ist. Zu diesem Zeitpunkt müssen alle bekannt gewordenen Fehlerrisiken beseitigt oder zumindest beherrschbar gemacht worden sein. Mit der Unterschrift unter das Freigabedokument bestätigt der Zulieferer zudem, dass er alles Erforderliche getan hat, um potenzielle Fehler zu erkennen und abzustellen.
Weil der Zulieferer genau dies getan hat, landet die Reklamation eines Fehlers an einem von ihm verantworteten Bauteil zunächst auch einmal folgerichtig über den OEM bei ihm. Denn eigentlich ist nach dem Produkthaftungsgesetz derjenige für den Fehler verantwortlich zu machen, der ein Produkt „in Verkehr“ gebracht hat. Das ist in der Automobilindustrie der OEM. Doch dieser kann die Verantwortung und somit die Haftung für Fehler auf die Lieferkette – bis zum Verursacher der Fehlfunktion – übertragen.
Die Voraussetzung dafür, dass Gesetzgeber und Behörden dies akzeptieren ist, dass der In-Verkehr-Bringende eines Produktes nachweist, dass er seiner Verantwortung auf andere Weise gerecht wird. Das geschieht durch die Etablierung eines Systems, das in die Lieferkette hineinwirkt. Dessen Regeln sind darauf ausgerichtet, Fehler zu vermeiden; dort, wo sie doch passieren, schnell und verlässlich abzustellen; Fehlerursachen sicher zu identifizieren und einem wiederholten Auftreten des Fehlers wirksam vorzubeugen. Hinzu kommt, dass Fehler oder Fehlfunktionen, die die Sicherheit des Produktes für Personen betreffen und die Einhaltung von Gesetzen und behördlichen Regeln tangieren, besonders sorgfältig behandelt werden. Dieses System zu etablieren ist im Kern die Daseinsberechtigung der IATF 16949.
Doch damit nicht genug der Regelungen und Verfahren. Was, wenn doch ein Fehler auftritt, der im unangenehmsten Fall der Fälle auch noch vom Verbraucher, dem Endkunden, entdeckt wird? Dieser lässt seinen Unmut wohl zunächst am Händler oder immer öfter am Support des Herstellers aus. Die Übertragung der Verantwortung auf die Lieferanten erlaubt dem Hersteller – wir erinnern uns an die Unterschrift unter das Freigabedokument – den Fehler oder die Fehlfunktion auch dort zu reklamieren. Jetzt ist es am Lieferanten nachzuweisen, dass die Verantwortung nicht bei ihm liegt – oder eben die Kosten zu tragen. Die sind in dieser Phase des Lebenszyklus eines Produktes dann meist sehr hoch. Unter dem Druck, der dadurch auf allen Beteiligten lastet, verlaufen solche Verfahren oft nicht sehr geschmeidig. Hier kann eine klare Regelung zu Rollen, Funktionen, Abläufen und Methoden unterstützen, wie sie im VDA-Band Schadteilanalyse Feld (SAF) festgehalten sind.
Weitere Vorteile kann eine Organisation erzielen, wenn sie auch unabhängig von konkreten Vorfällen über einen guten Fundus an Qualitätsdaten zu ihren Produkten verfügt – auch zu deren Verhalten im Feld. Das kann drohende Szenarien bereits erkennen lassen, noch bevor eine Reklamation eintrifft. Zudem beschleunigen Felddaten zur Produktqualität die Fehler- und Ursachenanalyse.
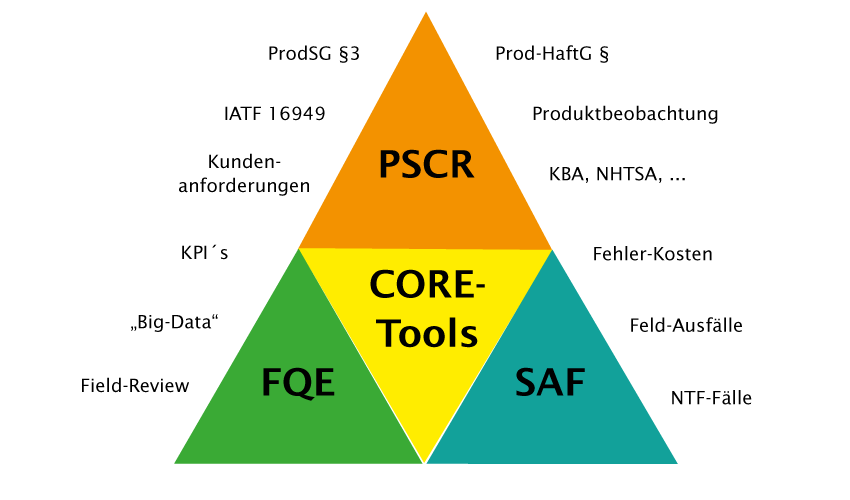
Vernetzung von Systemen, Daten und Methoden auf Unternehmensebene (eigene Abbildung)
Diese kurze Zusammenstellung zeigt auf, wie wichtig die Vernetzung einzelner Themen ist, wenn das QM-System seine volle Wirksamkeit entfalten soll. Das gilt umso mehr, wenn es unternehmensübergreifend gedacht wird. Für sicherheitsrelevante Themen und Gesetzeskonformität ist es Aufgabe des Product Safety & Conformity Representative (PSCR), eine solche Vernetzung auf Unternehmensebene herzustellen und auch als Kommunikator nach außen zum Kunden zu wirken. Er kann sich dabei auf die QM-Organisation stützen: die Qualitätsplanung und die Freigabedokumentation, Entwicklungsdaten und Prozessparameter. Aber ihm stehen auch Experten für Schadteilanalyse Feld (SAF) und Feld-Qualitätsdaten (FQE) zur Verfügung, die über Daten und Methoden verfügen, um Analysen und Maßnahmen schnell und zielgerichtet vorzunehmen.
In komplexen Systemen ist es erforderlich, Themen in ihrer Vernetzung zu betrachten und nicht als isolierte Anforderungen zu sehen. So leicht einem im Angesicht von Überregulierung ein „Was denn noch alles?“ von den Lippen kommen mag: Ein gutes Zusammenspiel der einzelnen Komponenten einer Organisation macht Komplexität auch unter belastenden Bedingungen, wie sie ein Reklamationsfall in der Regel bedeutet, beherrschbar.
Über den Autor: Jörn Cerff
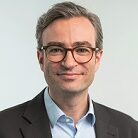