Industrie 4.0 – Zielsetzungen8 | 03 | 16
Andreas Altena und Sabine Roeb-Vollmer veröffentlichten im Herbst 2015 gemeinsam ein Whitepaper mit dem Titel „Sichere IT-Systeme und sichere Kommunikation: zwei neuralgische Herausforderungen für Industrie 4.0“. Im DGQ Blog nehmen wir das Thema genauer unter die Lupe. Es geht es um Begrifflichkeiten, Ziele und Herausforderungen im Kontext von Industrie 4.0, aber vor allem sollen zentrale Aspekte zur Qualitätssicherung, Standardisierung und Informationssicherheit vorgestellt werden. In den vergangenen Wochen haben wir zunächst einen Überblick über das Thema gegeben sowie wichtige Begriffe, wie Definitionen und Schlüsseltechnologien behandelt. Heute stehen die Zielsetzungen von Industrie 4.0 im Vordergrund.
Möglichkeiten durch Einsatz der Schlüssentechnologien
Die vier Kategorien technologischer Treiber, die Industrie 4.0 voranbringen haben wir bereits letzte Woche intensiv behandelt (hier nachlesen):
- Cyber-physische (Produktions-)Systeme (CPS und CPPS)
- Integrierte Daten und Big Data
- Cloud-Technologien
- Additive Fertigungsverfahren
Die beschriebenen Schlüsseltechnologien ermöglichen einen radikal veränderten Prozesse entlang der gesamten Wertschöpfungskette. Das Ziel ist eine sogenannte Smart Factory – wandlungsfähig, ressourceneffizient und ergonomisch.
Industrie 4.0: Kürzere Entwicklungszeiten und integrativer Entwicklungsansatz
Variable und flexible, dezentral gesteuerte Produktionsanlagen erlauben individualisierte Lösungen mit einem geringeren Mehraufwand zu produzieren und zu verkaufen. Zum Beispiel können die Eigenschaften von Produkten schon während der Entwicklungs- und Designphase getestet werden, was die Herstellung von Prototypen beschleunigt. Solche Simulationsverfahren, die sich in den vergangenen Jahren wesentlich weiterentwickelt haben, werden heute bereits u. a. in der Automobilindustrie genutzt. So lassen sich inzwischen nicht nur mehr einzelne Bauteile, sondern komplette Bauteilgruppen berechnen und optimieren. Der Trend geht sogar dahin, unterschiedliche Simulationsdisziplinen miteinander zu kombinieren (z. B. Strömungssimulation mit Festigkeitssimulation, Magnetfeldsimulation mit Thermischer Simulation). Dank schnellerer Rechner bzw. durch Einsatz von Rechen-Cluster lassen sich zudem die Simulationszeiten immer mehr verringern. Neben kürzeren Entwicklungszeiten ergibt sich darüber hinaus ein integrativer Entwicklungsansatz: Zulieferer und Hersteller arbeiten gemeinsam und parallel an der Produktentwicklung (Simultaneous Engineering). Im Ergebnis ist damit eine Kleinstserienfertigung bis hin zur „Losgröße 1“ ohne große Kostennachteile möglich.
Abhängigkeit von IT-Systemen und Informationssicherheit
Die oben beschriebenen Szenarien machen aber auch deutlich, wie sehr viel mehr als heute die Wertschöpfungsketten in Industrie 4.0 von hochverfügbaren und integren IT-Systemen abhängig sein werden. Deshalb muss die IT-Infrastruktur jedes Unternehmens betriebssicher genutzt werden – Stichworte sind hier Datenintegrität und Datenverlust – und es muss sichergestellt sein, dass die Anwendungen zur Verhinderung eines Produktionsstillstands stets einsatzbereit sind. Zu betrachtende Risiken sind etwa: Stromausfall, RZ-/Server-Ausfall, Netzwerkausfall, Attacken durch Schadprogramme (z. B. Stuxnet, Dudu und Flame) auf vernetzten Produktionsanlagen oder fehlerhafte Konfiguration von Maschinen (menschliches Versagen). Dementsprechend wird die Bedeutung von Informationssicherheit in Zukunft schon während der Planungs- bzw. Entwicklungsphase weiter zunehmen. Es gilt, eine digitale und organisatorische Sicherheit herzustellen, z. B. zur Vermeidung von Manipulation oder Diebstahl von vertraulichen Informationen. Die ISO 22301 (Business Continuity Management = BCM) und vor allem die ISO/IEC 27001 (Informationssicherheit) enthalten diesbezüglich bereits umfassende Herangehensweisen.
Das Internet der Dinge
Im Zusammenhang von Industrie 4.0 darf ein Stichwort nicht fehlen: Das Internet der Dinge (Internet of Things = IoT), das zwar dem gleichen Themenkreis rund um Digitalisierung angehört, aber gegenüber Industrie 4.0 einen anderen Schwerpunkt setzt. Das Internet der Dinge strebt an, die Lücke zwischen realer und virtueller Welt zu schließen. Das geschieht über „intelligente Gegenstände“, sogenannte mit einer Sensorik ausgestattete Wearables, die in letzter Konsequenz den „klassischen“ Computer überflüssig machen. Bekannte Stichworte sind in diesem Zusammenhang beispielsweise Smart Home und Smart Car. Im besten Fall ist sich der Mensch der IT nicht mehr bewusst. So wird in diesem Sinne gerade die Datenbrille erprobt, doch erscheinen viele Projekte noch sehr zukunftsfern.
Bei Industrie 4.0 liegt der Schwerpunkt auf der Machine-to-Machine-Kommunikation (M2M) in der Entwicklung, Logistik und Fertigungstechnik, was vielerorts bereits in unterschiedlichen Zusammenhängen praktiziert wird. Angesichts der angestrebten und weiter oben beschriebenen intelligenten Fabrik ist Industrie 4.0 aber auch Teil des Internets der Dinge.
Alle bereits veröffentlichten Artikel zum Thema finden Sie hier:
Die Autoren:
- Sabine Roeb-Vollmer, Partnerin der Altena-TCS GmbH
- Andreas Altena, Geschäftsführer Altena-TCS GmbH
Über den Autor: Sabine Roeb-Vollmer und Andreas Altena
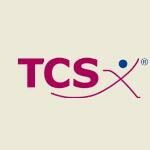
Sabine Roeb-Vollmer, Partnerin der Altena-TCS GmbH, selbstständig seit 1991, ist als Beraterin und DQS-Senior-Auditleiterin spezialisiert auf die Implementierung und Weiterentwicklung von Managementsystemen für Qualität, Informationssicherheit und Service Management. Sie war bereits in zahlreichen multinationalen Konzernen erfolgreich tätig, unterstützt aber auch gerne kleine und mittelständische Unternehmen bei deren Zertifizierungsvorbereitungen. Als systemischer Business- und Management-Coach für Führungskräfte, Projektmanager und Nachwuchsführungskräfte begleitet sie Menschen in Einzelcoachings. Als Coach ist sie Sparringspartnerin ihrer Klienten und unterstützt die persönliche Weiterentwicklung im Sinne von verbesserter Selbstreflexion und Leistungssteigerung und hilft bei der Lösung von Konflikten im beruflichen und privaten Kontext.
Andreas Altena, IT-Kaufmann und Betriebswirt, ist Geschäftsführer der Altena-TCS GmbH. Seine Kernkompetenzen sind Qualitäts-, Informationssicherheit-, Datenschutz- und (IT-)Service-Managementsysteme sowie Service Excellence. Über seine geschäftsführende Tätigkeit hinaus begutachtet er seit 2007 als DQS-Senior-Auditleiter Managementsysteme in den genannten Bereichen. Seit 2012 arbeitet er als Trainer und Experte für die DGQ-Weiterbildung in den Bereichen Qualitätsmanagement, Informationssicherheit und Auditorenausbildung. Er ist Autor und Mitautor von verschiedenen Veröffentlichungen rund um die Themen Managementsysteme, Risikomanagement und Informationssicherheit. Zu Themen des Datenschutzes und der Datensicherheit ist er ein gern gefragter Experte des regionalen Fernsehens.
Comments are closed.