Industrie 4.0 – Definition und Schlüsseltechnologien2 | 03 | 16
Gesucht: Eine allgemeingültige Industrie 4.0-Definition
Andreas Altena und Sabine Roeb-Vollmer veröffentlichten im Herbst 2015 gemeinsam ein Whitepaper mit dem Titel „Sichere IT-Systeme und sichere Kommunikation: zwei neuralgische Herausforderungen für Industrie 4.0“. Im DGQ Blog nehmen wir das Thema genauer unter die Lupe. Es geht es um Begrifflichkeiten, Ziele und Herausforderungen im Kontext von Industrie 4.0, aber vor allem sollen zentrale Aspekte zur Qualitätssicherung, Standardisierung und Informationssicherheit vorgestellt werden. Vergangene Woche haben wir bereits einen Überblick gegeben, heute widmen wir uns einer Definition und den Schlüsseltechnologien von Industrie 4.0.
Der Begriff „Industrie 4.0.“ wurde erstmals 2011 in einem Beitrag für die VDI-Nachrichten verwendet. Eine allgemeingültige und verbindliche Definition des Begriffs gibt es bis heute nicht. Die Erklärungen reichen, je nach Blickwinkel und Interessenlage, von einer volkswirtschaftlichen Programmatik zur Stärkung des Industriestandorts Deutschland bis hin zur Umsetzung von Teilaspekten der Digitalisierung und Automatisierung industrieller Wertschöpfung. Am weitesten verbreitet ist die Arbeitsdefinition der von der Bundesregierung, Wirtschaftsvertretern, Gewerkschaftern und Wissenschaftlern betriebenen Plattform „Industrie 4.0“:
Definition der Plattform Industrie 4.0
Am weitesten verbreitet ist die Arbeitsdefinition der von der Bundesregierung, Wirtschaftsvertretern, Gewerkschaftern und Wissenschaftlern betriebenen Plattform „Industrie 4.0“:
„Der Begriff Industrie 4.0 steht für (…) eine neue Stufe der Organisation und Steuerung der gesamten Wertschöpfungskette über den Lebenszyklus von Produkten. Dieser Zyklus orientiert sich an den zunehmend individualisierten Kundenwünschen und erstreckt sich von der Idee, dem Auftrag über die Entwicklung und Fertigung, die Auslieferung eines Produkts an den Endkunden bis hin zum Recycling, einschließlich der damit verbundenen Dienstleistungen.
Basis ist die Verfügbarkeit aller relevanten Informationen in Echtzeit durch Vernetzung aller an der Wertschöpfung beteiligten Instanzen sowie die Fähigkeit aus den Daten den zu jedem Zeitpunkt optimalen Wertschöpfungsfluss abzuleiten.
Durch die Verbindung von Menschen, Objekten und Systemen entstehen dynamische, echtzeitoptimierte und selbst organisierende, unternehmensübergreifende Wertschöpfungsnetzwerke, die sich nach unterschiedlichen Kriterien wie bspw. Kosten, Verfügbarkeit und Ressourcenverbrauch optimieren lassen.“
Schlüsseltechnologien und ihre Auswirkungen
In der Vision von Industrie 4.0 kommunizieren vernetzte Werkstücke, Maschinen und Anlagen miteinander – entweder via Internet oder über Inhouse-Netze. Viele dazu notwendige Technologien sind bereits vorhanden, aber erst durch die Nutzung ihrer Synergieeffekte ergibt sich das revolutionäre Produktionsparadigma.
Die technologischen Treiber, die Industrie 4.0 voranbringen, lassen sich dabei vier Kategorien zuordnen:
- Cyber-physische (Produktions-)Systeme (CPS und CPPS):
Miteinander vernetzte Maschinen und bewegliche Gegenstände, die mittels IT und kontinuierlichem Datenaustausch gesteuert werden. Das Produkt wird als intelligentes Werkstück zum aktiven Element im Produktionsprozess. - Integrierte Daten und Big Data:
Die Vernetzung von Maschinen und Objekten für alle verfügbaren Daten – über die verschiedenen Stufen der Wertschöpfungskette (horizontal) und zwischen den Akteuren der Zulieferkette (vertikal). Große Datenmengen werden erfasst, in Echtzeit analysiert und für die Prozessanpassung zurückgeführt (Big Data). - Cloud-Technologien:
Von jedem Ort aus Zugriff auf zentral gespeicherte Daten eines Prozesses über das Internet, die mittels bereitgestellter Verarbeitungs- und Analysesoftware bearbeitet werden können. - Additive Fertigungsverfahren:
3D-Visualisierung und 3D-Druckverfahren. Dadurch wird es in vielen Fällen möglich, aus druckbarem Material Bauteile mit variablen Formen zu fertigen.
Zusammengenommen ermöglichen die beschriebenen Schlüsseltechnologien mittels laufender Auswertung von Daten aus der Produktion, Qualitätssicherung und Prozessparameter radikal veränderte Prozesse entlang der gesamten Wertschöpfungskette. Ziel ist letztendlich die intelligente Fabrik (Smart Factory), die sich durch Wandlungsfähigkeit, Ressourceneffizienz und Ergonomie auszeichnet. Mit ihren variablen und flexibleren, dezentral gesteuerten Produktionsanlagen erlaubt sie, individualisierte Lösungen mit einem geringeren Mehraufwand zu produzieren und zu verkaufen.
Haben Sie den ersten Blogpost verpasst, in dem es um Begriffe, Ziele und Herausforderungen ging? Ersten Blogpost lesen
Die Autoren:
- Sabine Roeb-Vollmer, Partnerin der Altena-TCS GmbH
- Andreas Altena, Geschäftsführer Altena-TCS GmbH
Über den Autor: Sabine Roeb-Vollmer und Andreas Altena
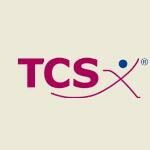
Sabine Roeb-Vollmer, Partnerin der Altena-TCS GmbH, selbstständig seit 1991, ist als Beraterin und DQS-Senior-Auditleiterin spezialisiert auf die Implementierung und Weiterentwicklung von Managementsystemen für Qualität, Informationssicherheit und Service Management. Sie war bereits in zahlreichen multinationalen Konzernen erfolgreich tätig, unterstützt aber auch gerne kleine und mittelständische Unternehmen bei deren Zertifizierungsvorbereitungen. Als systemischer Business- und Management-Coach für Führungskräfte, Projektmanager und Nachwuchsführungskräfte begleitet sie Menschen in Einzelcoachings. Als Coach ist sie Sparringspartnerin ihrer Klienten und unterstützt die persönliche Weiterentwicklung im Sinne von verbesserter Selbstreflexion und Leistungssteigerung und hilft bei der Lösung von Konflikten im beruflichen und privaten Kontext.
Andreas Altena, IT-Kaufmann und Betriebswirt, ist Geschäftsführer der Altena-TCS GmbH. Seine Kernkompetenzen sind Qualitäts-, Informationssicherheit-, Datenschutz- und (IT-)Service-Managementsysteme sowie Service Excellence. Über seine geschäftsführende Tätigkeit hinaus begutachtet er seit 2007 als DQS-Senior-Auditleiter Managementsysteme in den genannten Bereichen. Seit 2012 arbeitet er als Trainer und Experte für die DGQ-Weiterbildung in den Bereichen Qualitätsmanagement, Informationssicherheit und Auditorenausbildung. Er ist Autor und Mitautor von verschiedenen Veröffentlichungen rund um die Themen Managementsysteme, Risikomanagement und Informationssicherheit. Zu Themen des Datenschutzes und der Datensicherheit ist er ein gern gefragter Experte des regionalen Fernsehens.